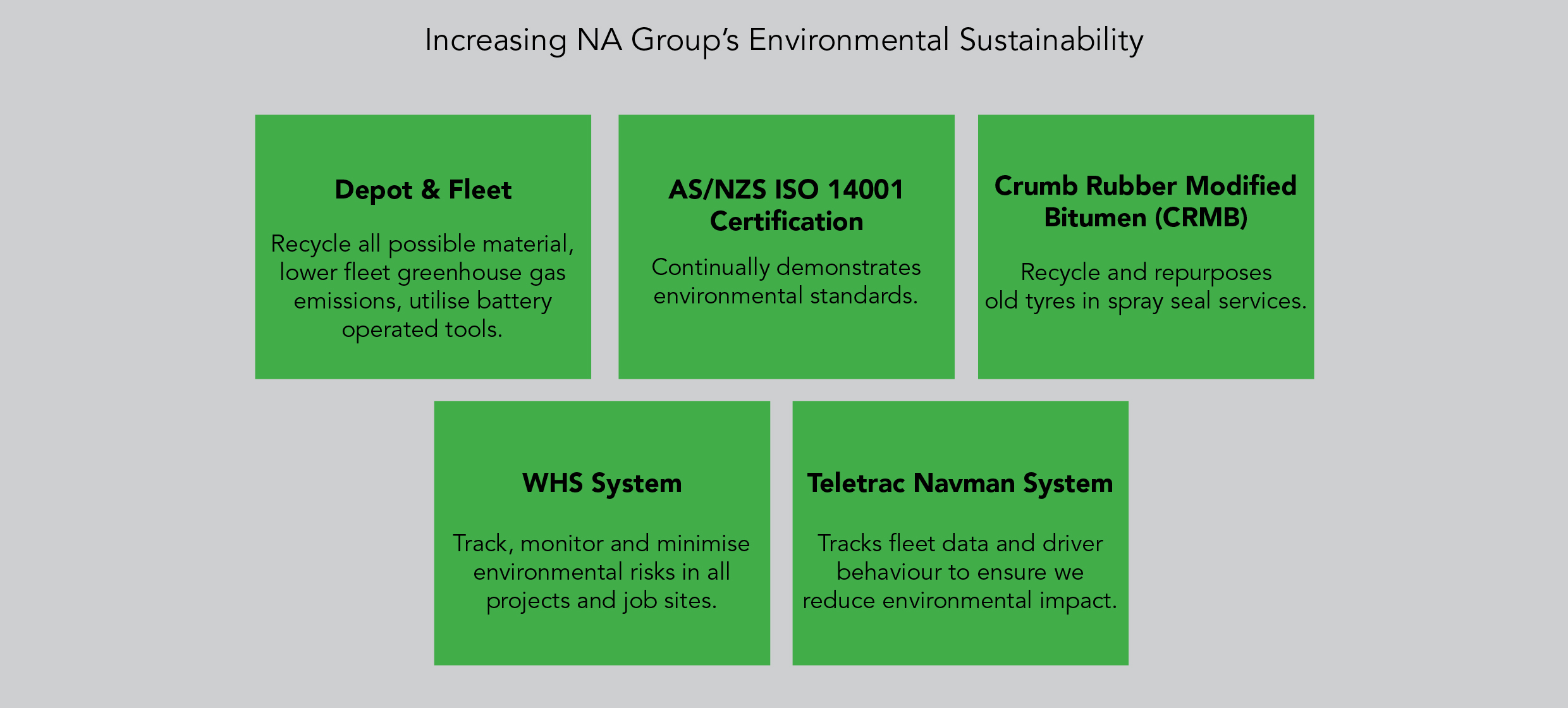
NA Group ensures we minimise our carbon footprint by continuously reviewing our work policies and procedures to warrant that we are performing using the most environmentally conscious methods available. To achieve this, we make changes through out depot and fleet policies, operating procedures, abide by our certification and review the products we use in our services.
Plant & Equipment
We recycle all possible material throughout our depot and the road construction process. We have begun upgrading various pieces of plant (as they fall due for upgrading) with higher emission controls. For example, our new innovative excavator models are specified to a higher European standard that delivers low greenhouse gas emissions. This process of more sustainable plant selection will continue as each plant asset requires upgrading.
Within our plant environment, we have introduced a process of identifying existing petrol-powered tools and equipment, and as these tools become due for renewal, they are replaced with battery powered models that reduce our carbon footprint. Examples of these tools include drills, demo saws, blowers, chainsaws, lighting & core holes. This is an ongoing process till all our tools and equipment have reached the end of their usage life and are replaced to battery powered models (where practical).
Our crew trucks have been fitted with lithium power packs to enable the crew to use power from the crew truck to run flashing lights, battery chargers, site lighting and other tools without the need for the truck to be left idling which reduces fuel usage and wear and tear. The lighting for our lighting towers has all been upgraded to LED from halogen to improve power efficiency. The workshop team has switched from engine oil to synthetic oils to provide extended engine service intervals.
All the processes and procedures that have been introduced to our plant and equipment will provide a pathway that reduces our overall business environmental footprint and allows us to function with increased sustainability.
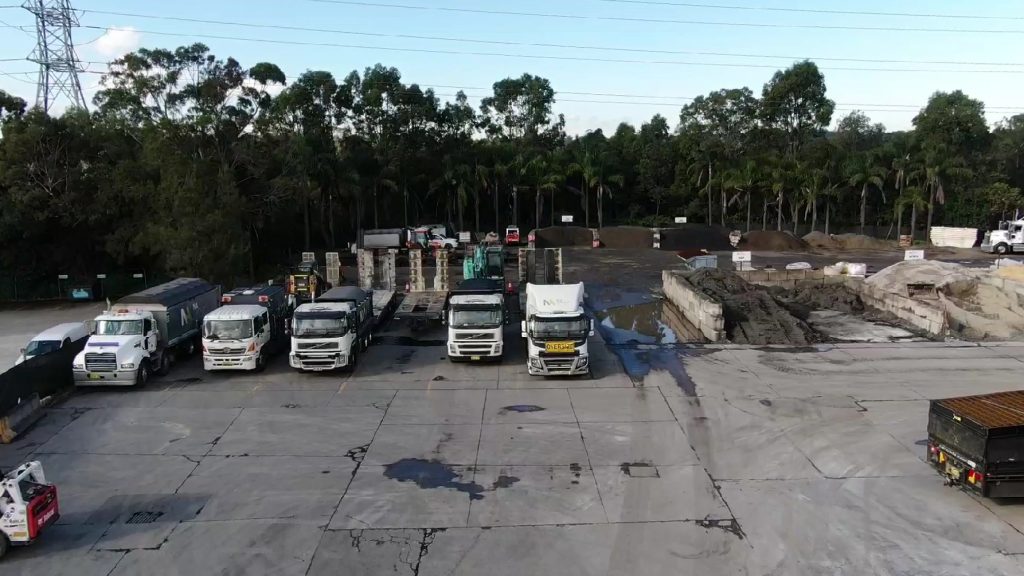
Certification
NA Group has attained the AS/NZS ISO 14001 Environmental management systems certification since 2012, continually demonstrating a standard that sets out our business requirements for an environmental management system. It has ensured we improve our environmental performance through efficient use of resources and reduction of waste, gaining a competitive advantage. More about NA Group certifications.
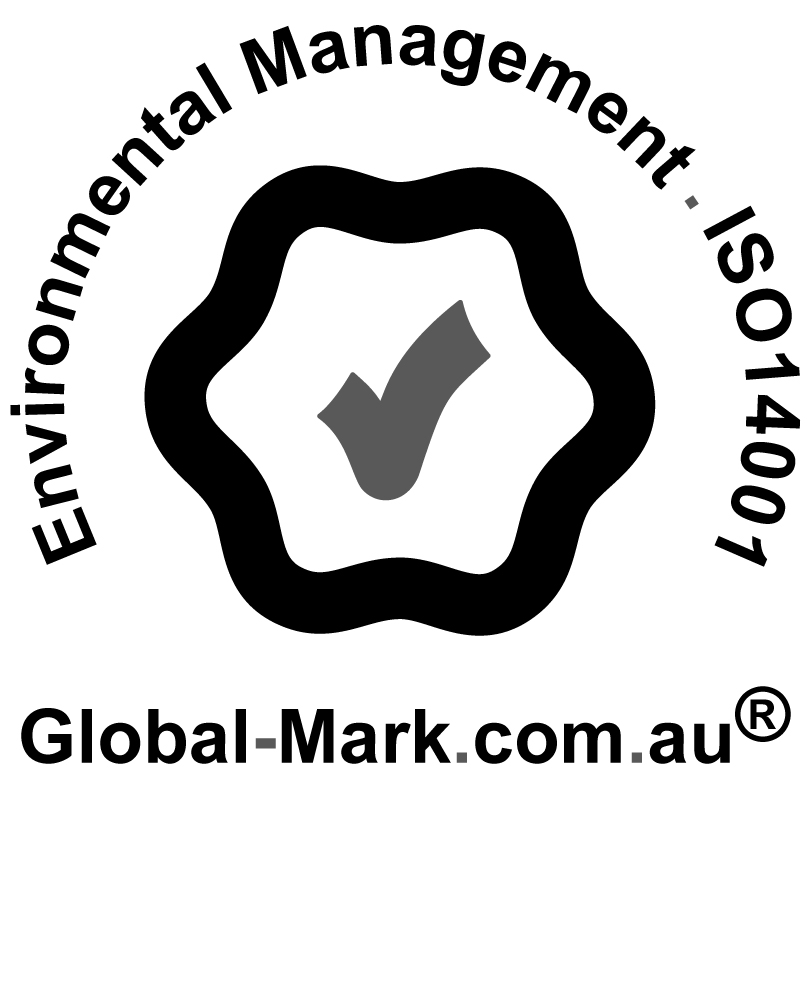
Turning Old Tyres into New Roads
With our continual drive to improve our carbon footprint, we decided to repurpose one of the world’s wastes that occupies large volumes of landfill space – car tyres. Traditionally, car tyres have been disposed of in several ways including in landfill or by burning them off. A single tyre takes approximately 50-80 years to decompose which causes a major space problem in landfill. By burning tyres, hazardous air pollutants are created, which can be dangerous and detrimental to the environment.
NA Group utilises Crumb Rubber Modified Bitumen (CRMB) which is a bitumen that combines crumbed recycled tyres within the heated bitumen that is sprayed on the road prior to the aggregate application. This provides the potential of repurposing and recycling hundreds of tyres in each spray seal application, saving tyres from going into landfill. This increases the environmental sustainability of our completed projects and reduces our carbon footprint as a business. Spray sealed road surfaces mixed with crumbed used tyres are also more elastic, durable and crack-resistant, which increases the longevity of the road.
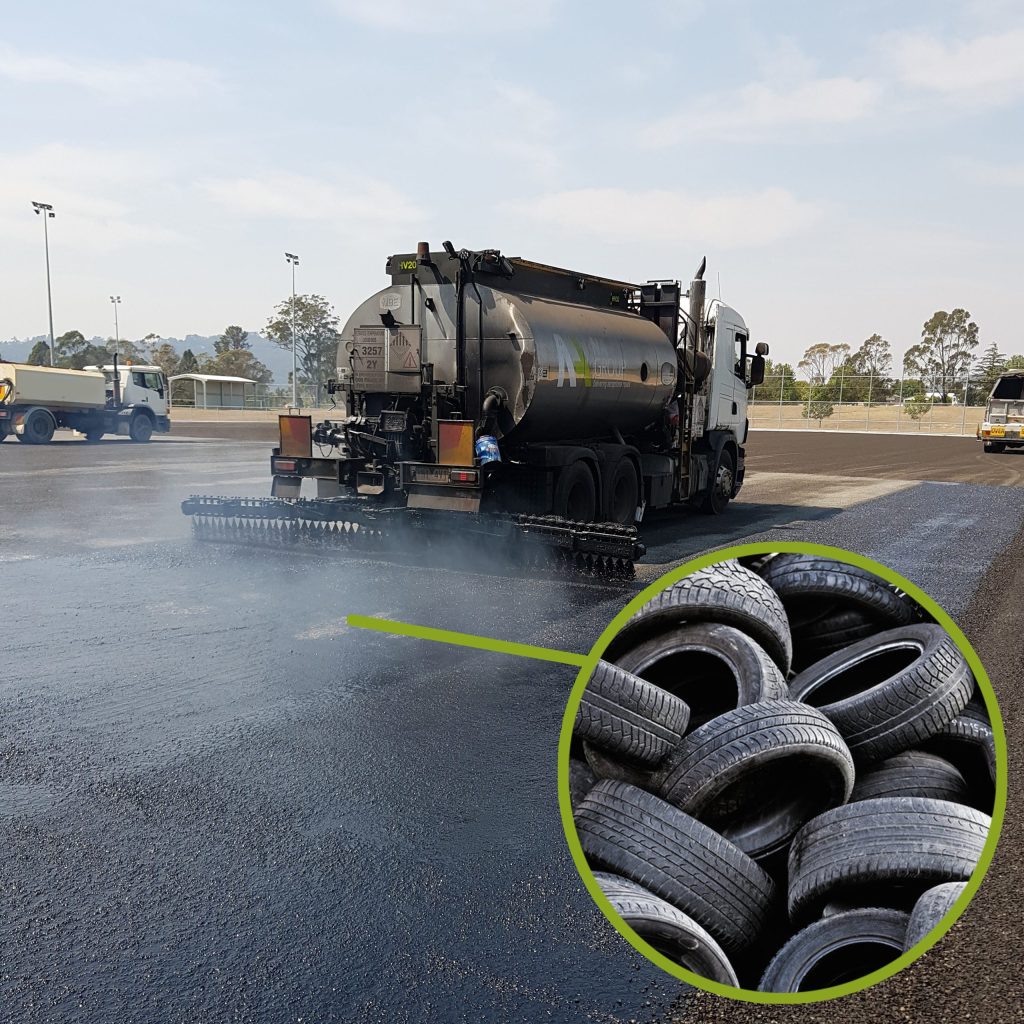
By recycling old tyres in our spray seal service, we contribute towards one of our core business values, to strive for environmental sustainability. More about our spray seal services.
WHS System
Our paperless WHS management system ensures updated project information are completed and accessible in real time by our clients. This ensures we effectively manage and control any environmental issues or risks for each project. Recently, we upgraded to a new platform called Dash Pivot. This is an ongoing process, and we are continuing to investigate and improve how we can utilise the platform through different aspects of the business. This new and improved system enables us to conduct the following business operations, paperless:
- Pre-start meetings and toolbox meetings.
- QA documentation / ITP’s.
- Diaries.
- Incident reporting / investigations / witness statements.
- Onsite safety inspections.
- Plant & machinery pre-starts.
- All machine service records.
- All plant, tools & equipment defects.
- Safe work method statements.
This upgrade has provided us with a more functional and easier method to track environmental risk and manage these more effectively at every project site.
This upgrade has provided us with a more functional and easier method to track environmental risk and manage these more effectively at every project site.
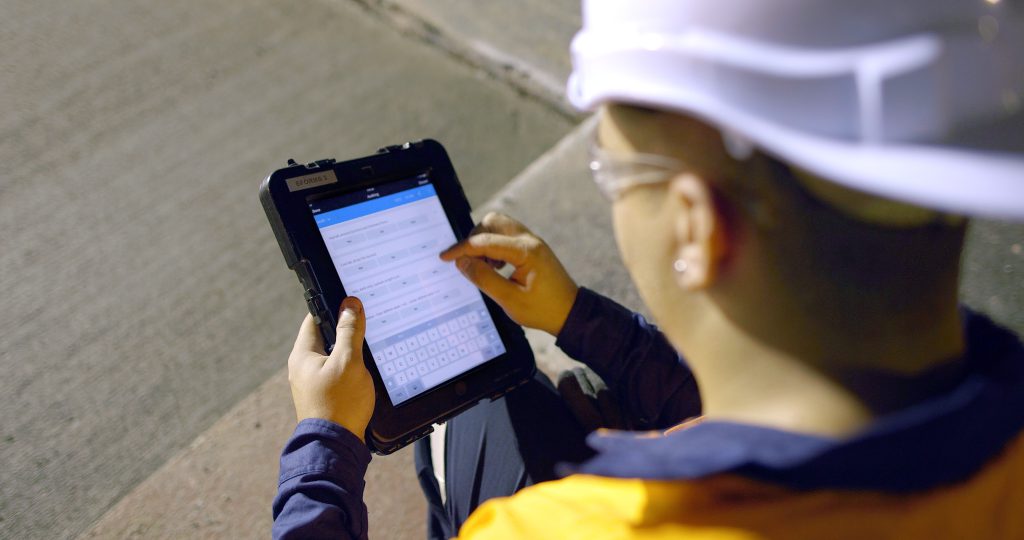
Teletrac Navman System
We have introduced a new GPS Fleet tracking system which is fitted to all our heavy vehicles. The system allows us to track a large range of data such as: fatigue management (monitoring drivers work / rest hours), speed breaches, vehicle maintenance schedules.
The system also allows us to monitor individual drivers and their driving habits that substantially contribute towards fuel usage levels. Drivers are given a live scorecard based on the following parameters: speed, harsh acceleration, harsh braking, harsh cornering, over revving, idle time.
The above parameters all contribute to a company scorecard, which is a relatively new feature to our systems and procedures. The scorecards help us to ensure that we achieve environmental objectives and targets such as fuel level usage and fleet wear and tear. By tracking and monitoring these measurements, we ensure that we do everything possible to minimise fuel usage, and that we maintain our fleet for a longer usage life to minimise the need for replacement. By being able to provide these indicators to our drivers, we provide a process that allows us as a business to identify driving behaviour and habits that can change to minimise fuel level usage.
The Teletrac Navman System assists us to monitor and actively minimise our overall environmental impact.
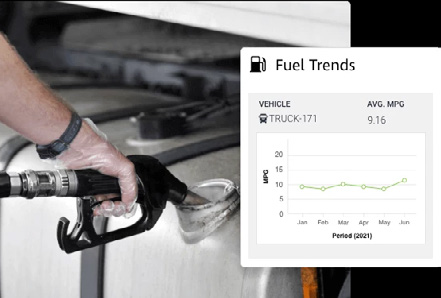